Grenland Rail - Connecting Locomotives
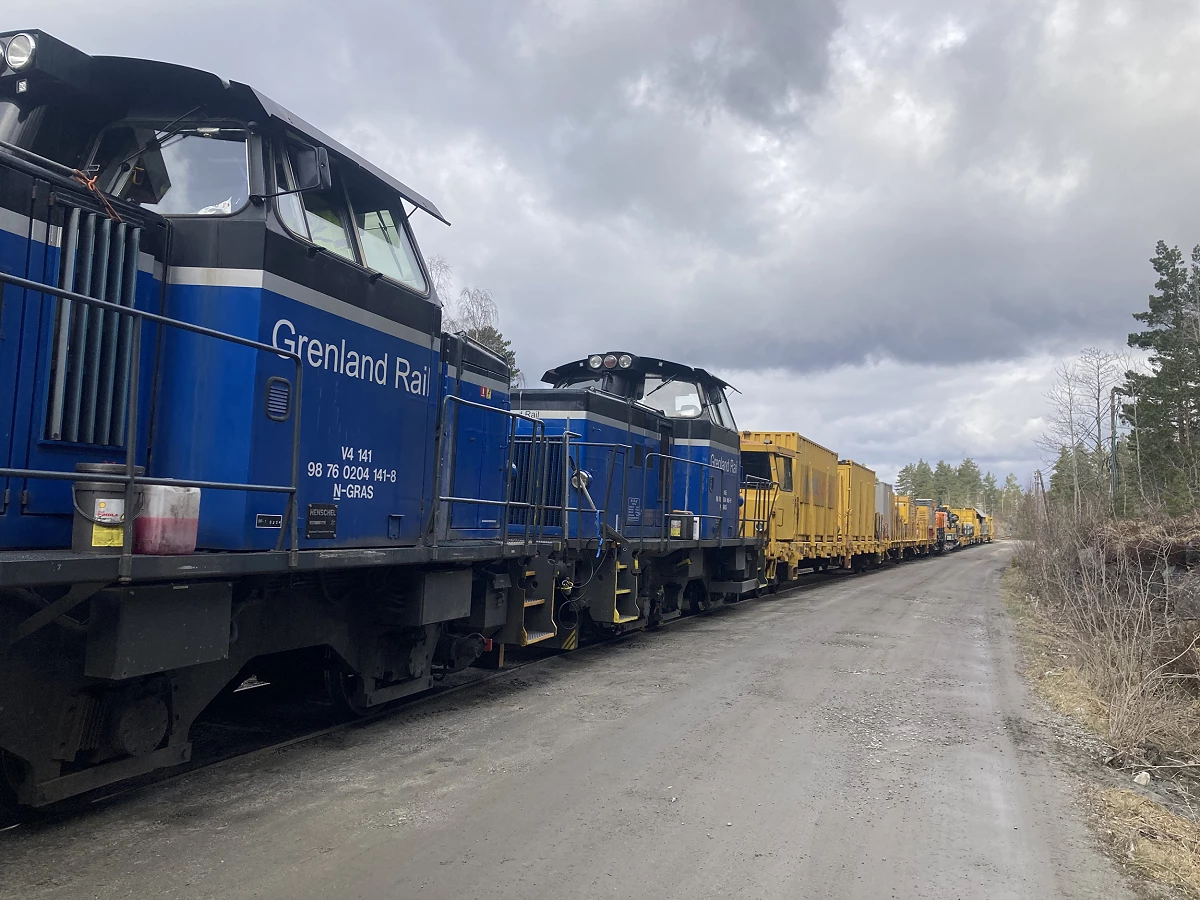
Grenland Rail AS is a company based in Skien, founded in 2005. Initially focused on providing machinery and equipment for track maintenance, the business has since expanded to include freight transportation. Today, they primarily operate across the entire railway network in Norway and Sweden.
We have previously collaborated with Grenland Rail and are thrilled to be working with them again.
Need for a More Flexible Solution
The project was initiated by Grenland Rail, focusing on the local "Kalken" route stretching from Vallermyrene to the Norcem cement factory in Brevik, approximately 10 km. The transport operates with two locomotives and two drivers. One locomotive is automatically controlled from the other via a cable-based system specific to the locomotive type, with the driver in the helper locomotive only for monitoring and safety. Our task was to develop a solution that allows different locomotives to connect regardless of fuel type or manufacturer. This solution will also be used for other routes operated by Grenland Rail.
PLC with Radio Link Solution
Our solution utilizes a PLC (Programmable Logic Controller) with two screens operated by separate control panels. An antenna is mounted on the locomotive to transmit essential information, including speed, temperature, engine speed, air pressure, and driver commands. This data is sent to the rear locomotive, equipped with similar components, allowing it to be remotely controlled and mirror the actions of the front locomotive. Simultaneously, the front locomotive receives information about temperature, engine load, and other relevant parameters to ensure no part of the train is overloaded.
In the long term, this solution will be implemented across various locomotive types, all capable of connecting together. The system operates in specific pairs, with each locomotive sending a unique ID that the leading locomotive can connect to. We have developed a check procedure to ensure the correct locomotives are paired through a pressure test. An air hose running through the entire train sends brake commands to the whole train set, and by adjusting this pressure, the driver can confirm the correct locomotive pairing.
Fun and Educational Process
"Fun" and "educational" are the words that come to mind for Einar Ottestad and Morten Hodne, who worked extensively on this project.
It was a complex process involving preliminary projects and multiple simulated tests to ensure everything worked correctly. While the goal was clear, the path to achieving it was less so. At Cody, we thrive on such challenges, leveraging a wide range of experience and expertise to find the best solutions.
There were numerous considerations, including various methods of communication with locomotives and ensuring components could withstand the harsh conditions within them. Locomotives experience temperatures ranging from -40 to +40 degrees Celsius, which our solutions had to endure.
Prepared for the Future
We have developed an enhanced and versatile version of existing technology. Our improvements have made the product more reliable by removing outdated systems. This solution is scalable and adaptable, helping to modernize and prepare locomotives for the future. With increasing demands and regulations on the electrification of transport and rail operations, our solution allows Grenland Rail to overcome fuel-type limitations.
The solution has been delivered and in use since April 2024. Practical use will reveal any further needs that may require additional development, concludes Morten.
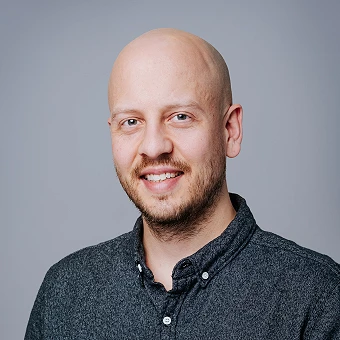
Magnus is our Chief Business Development Officer, and with his experience in both mechanical design, automation, project management, and sales, he has full control over what Cody can deliver. He also delves deep into the Machinery Directive, CE marking, and harmonized standards to ensure that what we deliver complies with laws and regulations.