How we work
We know what it takes and the path from idea to production! And you, as our customer, are with us every step of the way.
Tell us about your project
Meeting with the client
We'll start with you explaining a bit about what you need help with. In this meeting, we will likely ask many questions to get an overview of your needs and what might bring value to your business. The goal of the meeting is to determine if we can assist you and what the next steps would be if you choose to engage with us.
Insight phase
In the insight phase, we select team members with the most relevant expertise to delve deeper into mapping your needs and requirements. In some cases, this may be a small task, but in other cases, it could be a larger assignment that we address through one or more studies or feasibility projects
Concept phase
In the concept phase, Cody, in collaboration with you, will create proposals for how to solve the challenge, including sketches and general descriptions. A goal in this phase is often to establish a fixed price for the development and production of a prototype or a complete product. We don’t need to finalize the product before we can provide a price. Once we have agreed on a concept, we usually have enough information, combined with our experience in product development, to give you a price for the remaining work.
Development phase
Now that we have finalized the concept and have a clear goal for the outcome, we begin drawing up the details, selecting the right standard components, and determining how everything will function in detail. Once the detailed design is complete, we usually conduct a review with the customer to verify that it meets their requirements. The goal of this phase is to prepare for the procurement of components and parts.
Production phase
When a product is fully developed and approved, drawings of all components are sent to our suppliers for production. Plates need to be cut, components must be cast, machined, welded, etc. Then everything comes into our workshop in Skien for assembly. At this point, those of us who designed, developed, and programmed the product put on our work clothes and take the short walk through the offices and into the workshop.
Testing and approval
Once we have assembled the product, we conduct testing and fine-tuning of the equipment. Quality, speeds, and other parameters agreed upon with the customer earlier in the project are now checked. In projects where the customer desires it, they are often invited to come here and go through the final testing with us, known as a FAT (Factory Acceptance Test). We also carry out certification where required.
Delivery to client
Customers are located all over the country, so the delivery of equipment varies. Some items and machines can be shipped, and the customer installs them themselves. In other cases, we travel out to perform installation and commissioning. This is agreed upon in advance with you as the customer and determined together.
About us
We are an engineering firm that develops, designs, and builds custom production equipment—along with solutions in automation, robotics, and digital control systems. Our core competencies include mechanical design, robotics, control systems, automation, industrial IT, and complex system integration.
Get to know us better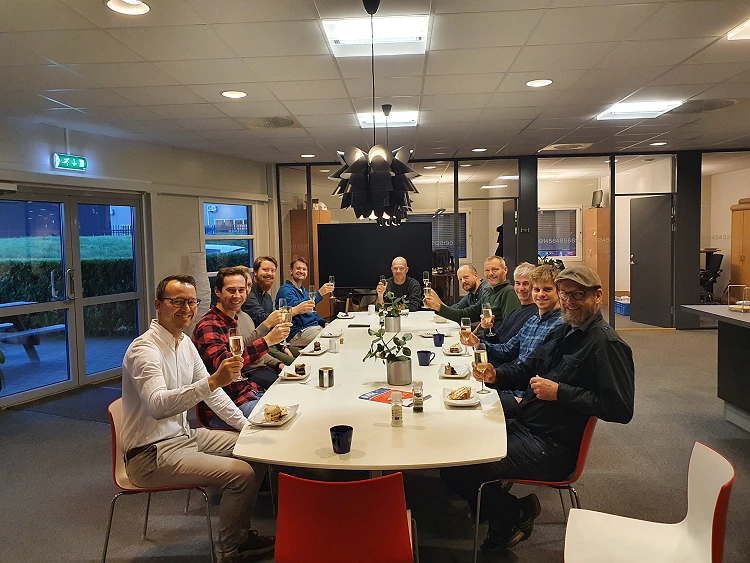