Revolutionizing Insulating Glass Production: Cody and Hybridized AS Leading the Way
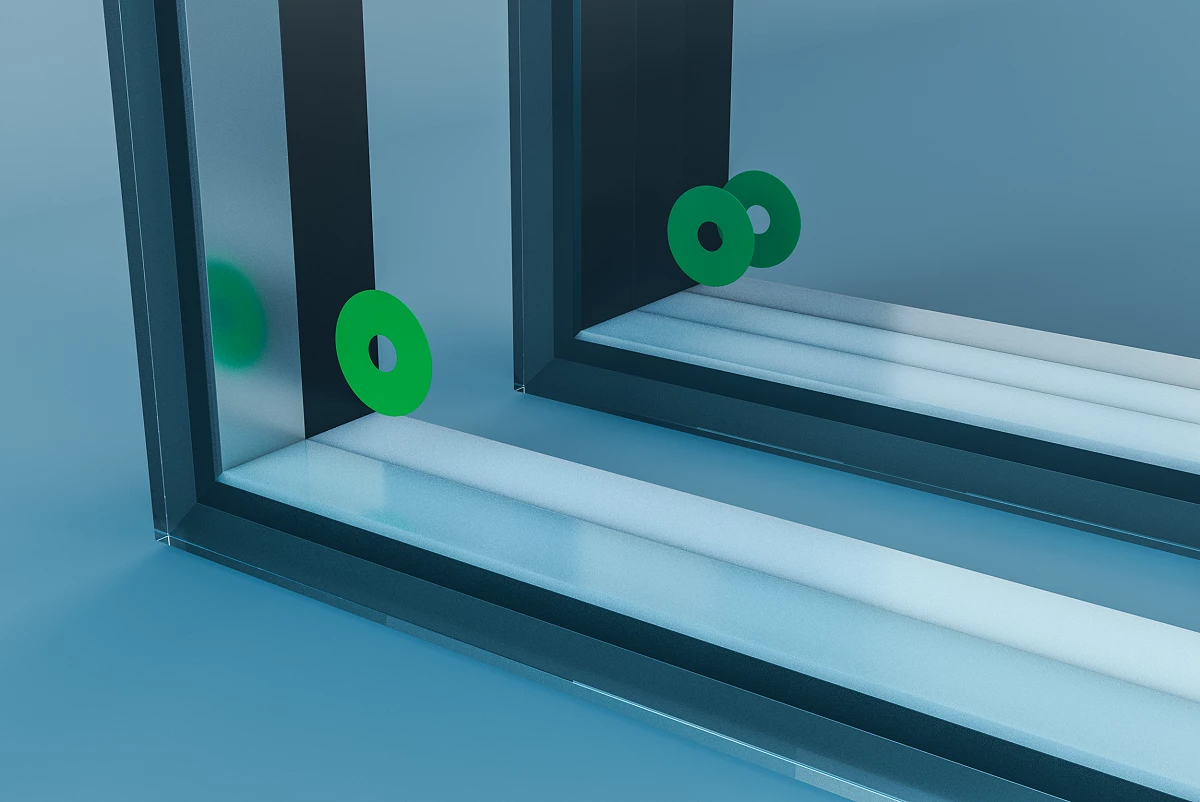
Hybridized’s Vision
Hybridized is working to rethink how insulating glass is produced—targeting a substantial reduction in energy use, raw material consumption, and CO₂ emissions. At the core of their concept is the replacement of thick inter-layer glass with ultra-thin PET foil, enabling lighter, more efficient glazing units.
The ambition isn’t just to invent smarter materials, but to ensure they can scale. The challenge has been production: integrating 0.07 mm film into standard manufacturing lines is technically demanding. So far, the process has remained mostly manual, slow, and energy-intensive—limiting consistency and scalability.
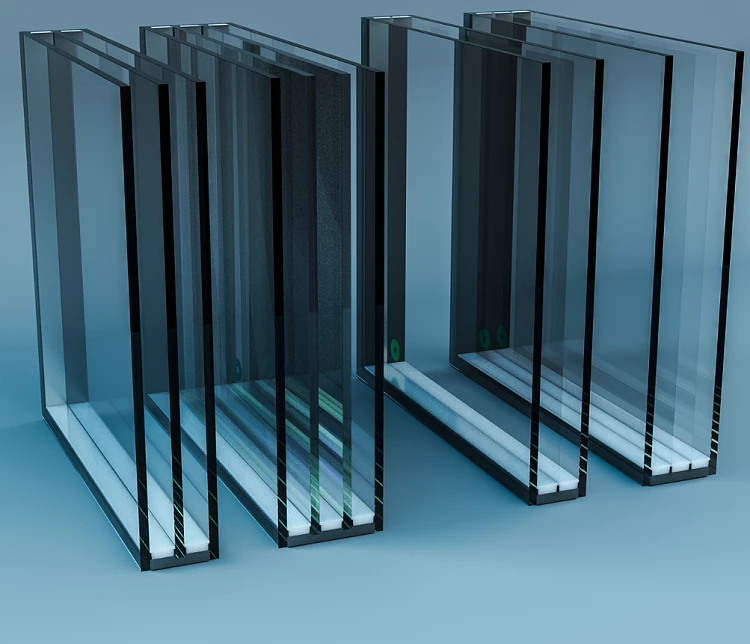
Our Role
Cody is developing a purpose-built automated production unit that handles ultra-thin PET foil with industrial precision—making it possible to manufacture Hybridized’s insulating glass on a scalable, reliable basis.
The system is designed to run as part of a real production environment—compact, modular, and adaptable to both new and existing lines. By automating this previously manual process, we’re eliminating a key barrier between lab-scale innovation and full-scale rollout.
“Bringing our hybrid glass technology into full-scale production has always been a critical milestone for Hybridized. I needed a production solution that would be scalable, reliable, and compatible with the realities of industrial manufacturing. That’s why our partnership with Cody has been so essential. Their deep understanding of automation and engineering has enabled us to take a visionary idea and transform it into a commercially viable solution.” – Atle Geving, Hybridized CEO
Driving Innovation in Production Automation
The shift from traditional 4–6 mm inter-layer glass to 0.07 mm PET foil isn’t just a materials innovation—it’s a leap in performance. The new hybrid glass units weigh up to 70% less than conventional triple-glazed windows and require 50% less glass to produce. That means lower emissions from both materials and transport, improved thermal insulation, and new design possibilities for energy-efficient buildings.
We’re building the automation that makes this possible. Precision handling. Seamless integration. Production speed fit for volume output. And above all: consistent quality at scale.
Initial tests in early 2024 confirmed the process works—and that it can be industrialized. Now we’re focused on refining and scaling the technology so it’s ready for real-world application.
Advancing EU Climate Goals Through Better Building Materials
Heating and cooling are the biggest energy consumers in buildings—and insulating glass is a weak link. Hybridized’s solution directly addresses that, offering a way to cut energy demand while reducing the environmental impact of the product itself.
It’s aligned with the EU’s Renovation Wave and broader climate goals: better-performing buildings, reduced emissions, and smarter use of resources. Scalable insulating glass with a smaller footprint could become a key enabler for the next generation of sustainable construction across Europe and beyond.
From Pilot to Production
In summer 2024, Hybridized signed a long-term strategic partnership with Nordan Vinduer—one of Northern Europe’s leading window manufacturers.
Backed by Innovation Norway and the Telemark Development Fund, this project represents a significant step forward—not just in glass manufacturing, but in how we engineer for sustainability.
“With this project, Cody's focus isn’t just on building machines—we’re enabling Hybridized to scale up energy-efficient glass production in a way that’s both cost-effective and commercially viable. By cracking the code on the insulated glass structure itself, we’ve removed a major barrier to automating the process. That dual approach is what makes this such a meaningful collaboration. Hybridized has a strong vision for sustainable window technology, and we’re proud to assist in bringing it to market.” – Ken André Myhra Kihle, Cody CEO

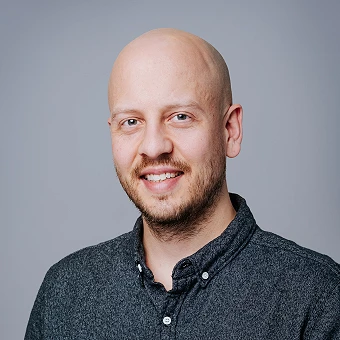
Magnus is our Chief Business Development Officer, and with his experience in both mechanical design, automation, project management, and sales, he has full control over what Cody can deliver. He also delves deep into the Machinery Directive, CE marking, and harmonized standards to ensure that what we deliver complies with laws and regulations.