GE HealthCare: Syringe loading machine
GE Healthcare has trusted Cody for 15+ years. This time, they needed a new machine for multiple syringe sizes—we developed, documented, and delivered a tailored solution.
The machine had to fit a tight cleanroom—without tearing down walls. We designed a compact unit, split for easy transport and reassembly inside.
Every detail was designed, documented, and reviewed to meet strict pharma and GMP requirements. Precision and compliance are built in.
Delivered
Delivered by
Delivered by Cody
At Cody, we have been providing advanced machine solutions to GE for over 15 years. The syringe loading machine is one of them.
GE Healthcare is one of the world's leading innovators in medical technology and diagnostics, with over 50,000 employees worldwide. In Norway, they have factories in Oslo and Lindesnes and are one of Norway's most important export companies. At Cody, we have been providing advanced machine solutions to GE for over 15 years.
Pharmaceutical players demand high standards for machines and documentation. Production must be documented for both customers and authorities. Therefore, it is crucial for us at Cody to be a partner who understands these requirements.
Crucial that the machine fit into the cleanroom
This project focused on a production line that fills syringes with contrast agent for MRI and radiography. Initially, the standard was to fill only 20 ml units, but there arose a need to also fill 5- and 10 ml sizes. To accommodate filling other formats, a new machine was required to fit into the existing production line. In the same production series, there are many machines. One of them was delivered by us about 15 years ago, and it still functions well today.
Some major challenges included limited space and narrow doors leading to the position where the machine was to be placed. One option was to tear down a wall into the cleanroom, but this would have required recertification of the cleanroom, which is a cumbersome and costly process. Therefore, we chose to design a very compact machine that can be split in the middle so that each part can be transported through standard doors and easily assembled inside.
For machines located in a cleanroom, there are generally high requirements for design. Surfaces should be smooth, and there should be no visible screws or wires. These were part of the requirements we worked from.
As the machine was to replace another machine in an existing line, it was important that the machine physically fit with adjacent machines. Therefore, 3D scanning of existing space was carried out to ensure design and interface quality in the design process.
Unpacking of empty syringes
The machine receives sealed boxes of sterile syringes, and for them to be filled with contents, the unpacking process must take place in an environment with strict cleanliness requirements. The machine is designed to ensure a laminar airflow along surfaces to prevent the swirling of particles, and the cleanliness of the air is continuously monitored.
On the right side, sealed boxes enter the machine. Sealing lids are removed and sent out of the machine through a chute. Then, the grid with the syringes is lifted out and placed in a station where the syringes are lifted by a fork mechanism. The syringes are then pushed off the fork and onto two vibrating tracks to the filling machine, which is the next step in the process. The grid that held the syringes is sent out a chute on the left side of the machine, and the empty syringe box is sent out again on the right side of the machine to an automatic stacking station.
Through the operator panel, one can control and monitor the production and select programs for the various syringe sizes.
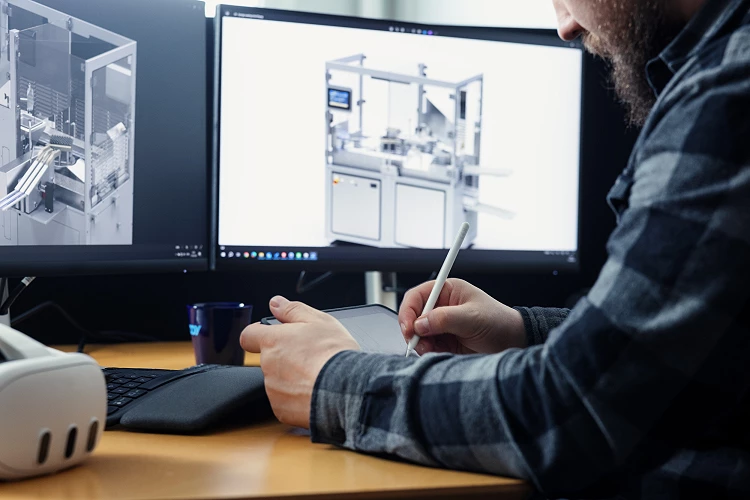
Documented design process
GE approached us with a specification requirement and a desire for a new machine. We proposed several different designs and eventually settled on a machine that we could offer and that met the requirements. The design was thoroughly documented to ensure that all requirements were met. There were also several rounds of feedback and comments from the customer on the solutions along the way.
Small space
"What was particularly challenging and interesting about this machine was that we had to perform a lot of operations in a very small area. This means that we had to have full control over all movements in the machine so that different parts do not collide with each other - almost like a sliding puzzle," says project manager at Cody, Jared Hansen.
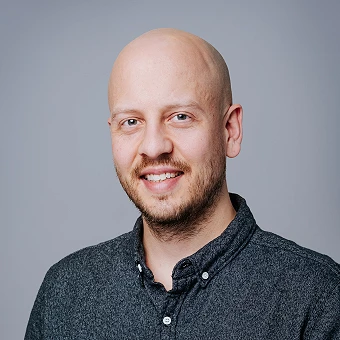
Magnus is our Chief Business Development Officer, and with his experience in both mechanical design, automation, project management, and sales, he has full control over what Cody can deliver. He also delves deep into the Machinery Directive, CE marking, and harmonized standards to ensure that what we deliver complies with laws and regulations.